Understanding Hydraulic Oil Filler Caps: Key Insights
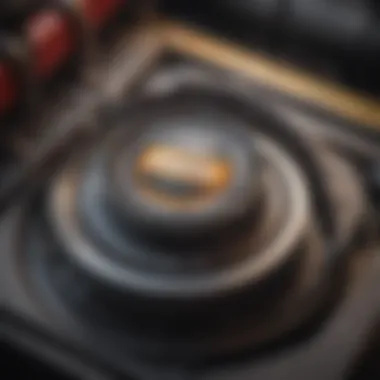
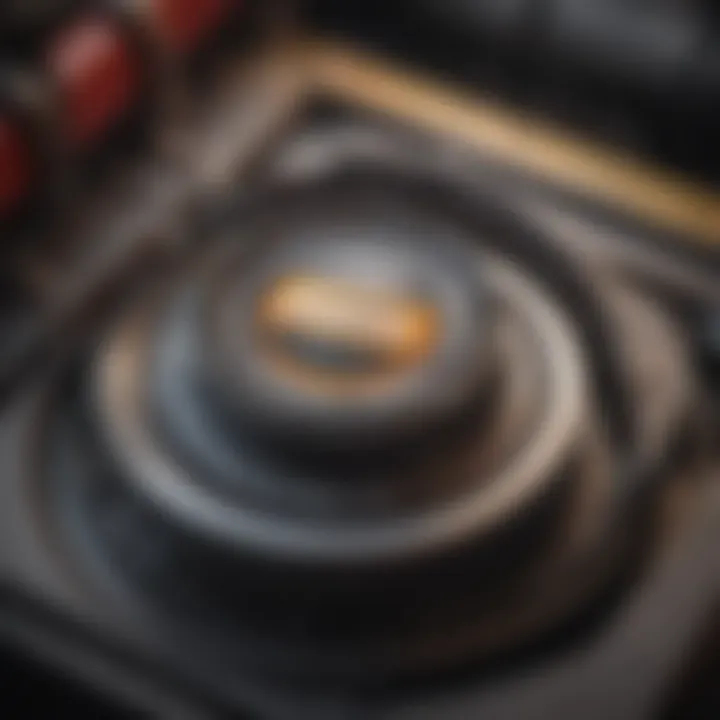
Intro
Hydraulic systems play a vital role in a variety of machinery and vehicles, primarily due to their efficiency and load-bearing capabilities. One often overlooked component of these systems is the hydraulic oil filler cap. Understanding the functions and maintenance of these caps can significantly improve the performance and longevity of hydraulic systems. The hydraulic oil filler cap is not just a protective enclosure; it serves essential functions that contribute to the smooth operation of hydraulic machinery.
In this article, we will explore the integral role of hydraulic oil filler caps. Topics of discussion will include their functions, maintenance practices, and applications in sectors such as agriculture and horticulture. We will highlight current trends in these industries, the importance of sustainable practices, and effective gardening techniques to help professionals and enthusiasts alike.
Latest Trends in Agriculture
Overview of Current Trends
Agriculture is undergoing a significant transformation due to advancements in technology and a growing focus on sustainability. These trends are influencing not only production methods but also the tools and equipment used in farming.
One notable trend is the integration of precision farming techniques. This approach utilizes data analytics and sensor technology to optimize crop yields while minimizing resource waste. Farmers are using hydraulic systems in various machinery that benefits from higher efficiency and improved performance. For example, tractors equipped with advanced hydraulic systems allow for better control and responsiveness in the field.
Impact of Technology on Farming Practices
Technologyβs impact on farming practices cannot be overstated. Hydraulic oil filler caps, for instance, are designed to ensure the safe storage and proper circulation of hydraulic fluid, which is vital in machinery operations. In modern farming, where quick adaptability is essential, the reliability of hydraulic systems is crucial. As farmers adopt new technologies, the design and materials used in hydraulic oil filler caps are also evolving. This ensures that they can withstand harsher conditions and facilitate better maintenance.
Sustainable Practices: Towards a Greener Future
Importance of Sustainability in Agriculture
Sustainability is increasingly becoming a priority in agricultural practices. With the threat of climate change and the need for responsible resource management, farmers are seeking ways to implement more sustainable techniques. The importance of maintaining hydraulic systems cannot be overlooked in this context. An efficient hydraulic system contributes to reducing energy consumption and resource waste.
Methods for Sustainable Farming
Farmers can adopt several methods to promote sustainability:
- Crop rotation: This practice enhances soil health and reduces the risk of pest infestations.
- Integrated pest management: Using biological controls instead of chemicals benefits the ecosystem.
- Water conservation techniques: Efficient irrigation systems decrease water consumption.
- Regular maintenance of hydraulic equipment: Proper upkeep reduces waste and prolongs equipment life. Utilizing hydraulic systems effectively ensures they operate at optimal levels.
Gardening Techniques and Tips
Essential Gardening Tools and Equipment
Effective gardening requires the right tools. Some essential tools include shovels, rakes, pruners, and of course, equipment powered by hydraulic systems, such as tillers and tractors. Each tool serves a specific purpose, improving efficiency and reducing physical strain on the gardener.
Seasonal Gardening Practices
Different seasons require tailored gardening practices. For spring, gardeners may focus on planting and preparing soil, while summer may focus on watering and pest management. During the fall, it is essential to prepare gardens for winter, which includes clearing debris and possibly utilizing machinery to till the soil.
"Regular maintenance of hydraulic systems not only improves efficiency but also prolongs the lifespan of equipment."
Preface to Hydraulic Systems
Hydraulic systems play an essential role in the functionality of modern machinery. These systems leverage pressurized liquids to transmit power, which enables a wide range of applications in various industries. Understanding hydraulic systems is vital, especially when focusing on specific components like hydraulic oil filler caps. Hydraulic oil acts as the lifeblood of these systems, facilitating movement and efficiency. Thus, recognizing how hydraulic oil filler caps contribute to the overall system's performance is crucial.
Definition of Hydraulic Systems
A hydraulic system is defined as a mechanism that uses incompressible fluid to transmit force. It consists of several interconnected components, including the pump, actuators, hoses, and, importantly, the hydraulic oil filler cap. The fluid is pressurized through a pump and transmitted through hoses to create mechanical movement, powering equipment such as tractors, excavators, and other machinery.
Importance in Agriculture and Horticulture
In the context of agriculture and horticulture, hydraulic systems enhance productivity and efficiency. They are used in various machines, such as tractors, seeders, and harvesters. The precise control hydraulic systems offer allows farmers to perform tasks that require significant force with minimal effort. Moreover, the hydraulic oil filler cap ensures that the hydraulic oil remains contained, maintains appropriate pressure, and prevents contaminants from entering the system. The reliability of hydraulic systems directly impacts productivity, making knowledge of these systems vital for farmers and enthusiasts aiming to maximize their machinery performance.
"Hydraulic systems are fundamental in modern agriculture, translating hydraulic energy into efficient, powerful operations throughout the entire farming process."
Effective management of hydraulic systems, including the maintenance of oil filler caps, not only prolongs equipment life but also ensures that agricultural tasks can be carried out smoothly and efficiently.
Components of Hydraulic Systems
Understanding the components of hydraulic systems is essential for anyone involved in agriculture and horticulture machinery. These components work in unison to create an effective hydraulic system capable of performing various tasks. Each part plays a critical role in ensuring efficiency and reliability in the operation of heavy machinery. Emphasizing the significance of these components helps the reader appreciate how hydraulic systems function and their importance in agriculture.
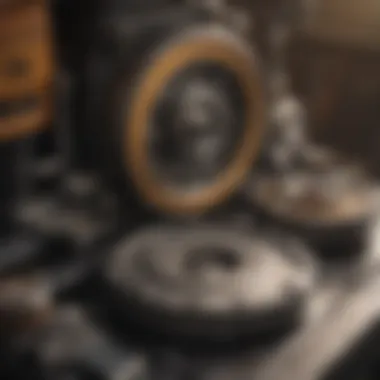
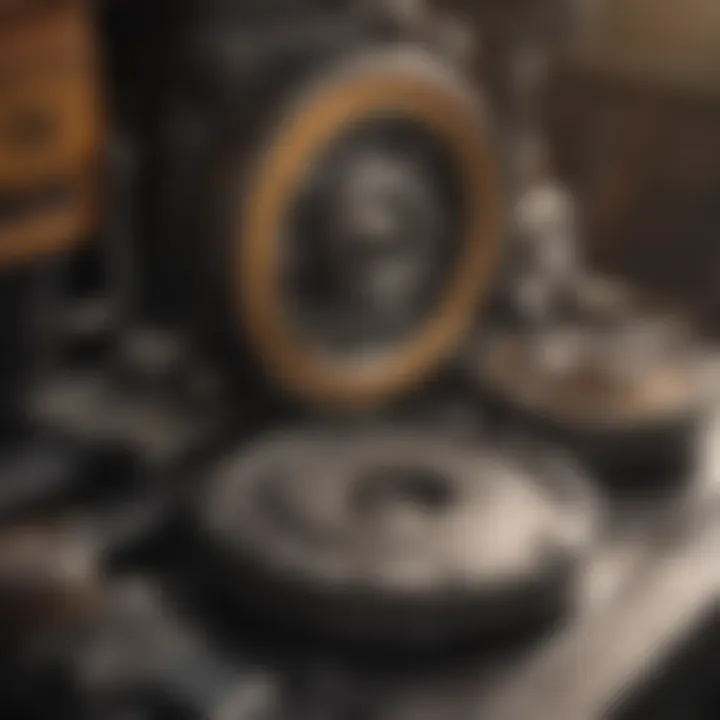
Pump
The pump is the heart of any hydraulic system. It converts mechanical energy into hydraulic energy by moving hydraulic fluid through the system. In agricultural machinery, reliable pumps are crucial as they ensure the timely and effective execution of tasks such as plowing, planting, or harvesting.
Common types of pumps include gear pumps, vane pumps, and piston pumps. The selection of the appropriate pump depends on the specific application, such as the required flow rate and pressure. A malfunctioning pump can lead to substantial decreases in efficiency, making understanding its role vital.
Actuator
Actuators convert hydraulic energy back into mechanical energy, allowing machines to perform work. In hydraulic systems, actuators may include hydraulic cylinders and motors. The latter is particularly important for converting fluid pressure into rotational motion.
In agricultural equipment, actuators operate components such as lifts, steering systems, and turning mechanisms. The effectiveness of these machine features directly relies on the proper functioning of the actuators, making them a cornerstone of hydraulic application.
Hoses and Fittings
Hoses and fittings connect various components of hydraulic systems. These elements carry the high-pressure hydraulic fluid and must withstand extreme pressures and temperatures. Quality hoses and fittings are essential to prevent leaks and ruptures, which can lead to equipment failure and costly repairs.
Materials used for hoses can vary, such as rubber or thermoplastic. The choice often depends on the operational environment and specific machine requirements. Regular inspections and maintenance of hoses and fittings ensure that they remain in good condition, enhancing the hydraulic system's overall efficiency.
Hydraulic Oil Filler Cap
Hydraulic oil filler caps, though small, play a significant role within hydraulic systems. These caps serve multiple essential functions. They seal the hydraulic reservoir to prevent fluid loss while ensuring the system maintains the necessary pressure. Additionally, they safeguard against contaminants that may compromise the fluid quality.
The design and quality of hydraulic oil filler caps can also influence system performance. An inadequate cap may lead to leaks or contamination, impacting the hydraulic system's efficiency and longevity. Therefore, understanding their construction and maintenance is a vital aspect of maintaining hydraulic systems in agriculture.
Role of Hydraulic Oil Filler Caps
Hydraulic oil filler caps play a vital role in the efficient functioning of hydraulic systems. These components are more than simple covers; they contribute significantly to the overall performance and longevity of hydraulic machinery. Properly functioning filler caps ensure that the hydraulic fluid remains contained, maintaining both the effectiveness of the system and its safety. Additionally, they offer protection against various external elements that can compromise system integrity, thereby enhancing operational reliability.
Primary Functions
Fluid Retention
Fluid retention is a fundamental function of hydraulic oil filler caps. These caps are designed to keep hydraulic oil secure within the reservoir. This is important as hydraulic systems rely on adequate fluid levels to function correctly. Without proper fluid retention, there could be leaks, leading to inadequate lubrication and potential system failure. One key characteristic of fluid retention is its ability to create a sealed environment that prevents fluid loss to the atmosphere. This quality makes it a popular choice for ensuring system efficiency.
Moreover, fluid retention caps often come with rubber or silicone seals that enhance their sealing capabilities. This unique feature helps maintain a stable pressure within the system, reducing the chances of air ingress, which could introduce bubbles that impair performance. However, over time, seals can degrade, requiring regular inspection to ensure optimal performance of the cap.
Pressure Maintenance
Pressure maintenance is another critical function of hydraulic oil filler caps. Hydraulic systems operate under specific pressure levels; thus, maintaining this pressure is essential for effective operation. The caps are designed to withstand and maintain pressure, ensuring hydraulic fluid remains stable during system operation. A significant characteristic of pressure maintenance caps is their robust construction that can handle fluctuations in pressure.
This ability to maintain pressure is beneficial, as it prevents cavitation and enhances the responsiveness of hydraulic systems. Typically, these caps can feature a pressure relief valve that helps regulate the pressure within the reservoir. While this is an advantage, one must consider that any malfunction of this mechanism can lead to excessive pressure buildup, potentially resulting in catastrophic failures.
Contaminant Prevention
Contaminant prevention is a vital role of hydraulic oil filler caps. These caps serve as a barrier against dirt, dust, moisture, and other foreign particles that can compromise hydraulic fluid quality. A significant characteristic of contaminant prevention is its direct impact on the longevity and efficiency of hydraulic systems. When contaminants enter the hydraulic system, they can lead to blockages, increased wear, and reduced lubrication efficiency.
Filler caps with advanced sealing mechanisms are particularly effective in preventing contaminants from penetrating the system. This unique feature not only enhances maintenance intervals but also ensures that the hydraulic fluid retains its optimal viscosity and performance characteristics. However, contamination can still occur if the caps are incorrectly installed or damaged, which underscores the importance of regular inspection and maintenance.
Types of Hydraulic Oil Filler Caps
Hydraulic oil filler caps are available in various designs, each serving specific needs within hydraulic systems. Understanding these types aids in selecting the right cap for particular applications.
Standard Caps
Standard caps are the most common type used for hydraulic systems. They fit securely on the oil reservoir neck, providing a straightforward sealing solution. Their simplicity makes them a beneficial choice for many applications. A key characteristic of standard caps is their ease of use; they can be tightened or loosened without special tools. This feature allows for quick fluid checks or changes, making maintenance convenient.
However, while standard caps are effective for basic sealing, they may not provide pressure relief, which can be a disadvantage in high-pressure hydraulic systems. They require vigilant monitoring to ensure that there is no fluid loss or contamination.
Vented Caps
Vented caps are designed to allow air exchange while preventing fluid loss. This feature is key for systems that experience pressure fluctuations. The unique aspect of vented caps is their ability to maintain a balanced pressure environment within the reservoir, facilitating efficient hydraulic operation.

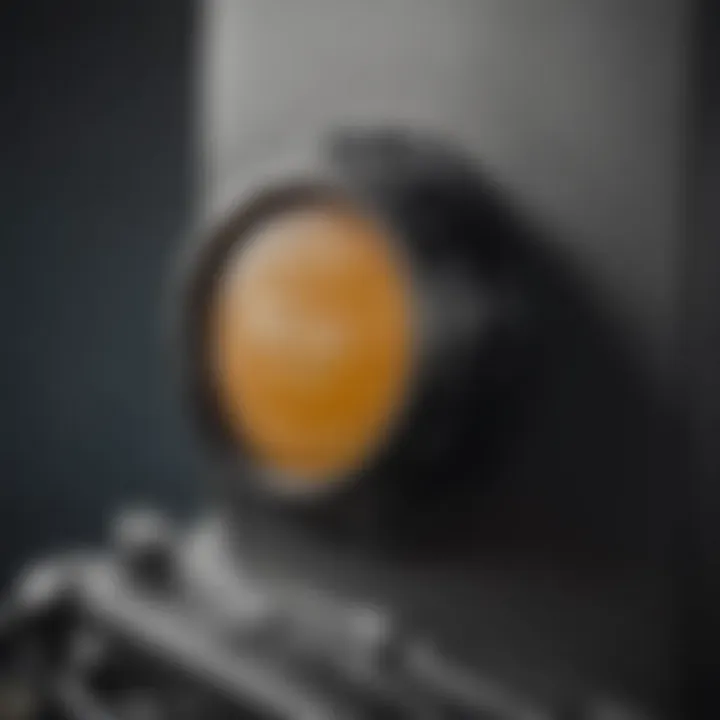
Their primary advantage is the prevention of vacuum buildup, which can hinder fluid flow. They also assist in regulating the fluid level, ensuring that hydraulic systems operate smoothly. However, caution is necessary, as vented caps can be susceptible to contaminants entering the system if the venting mechanism is poorly designed or maintained, warranting regular checks.
Quick Release Caps
Quick release caps are specialized for applications that require rapid access to hydraulic fluid. They are designed for efficiency, allowing for quick and easy removal without the need for tools. Their key characteristic is the user-friendly design, which accommodates fast fluid changes in various applications.
Quick release caps can be particularly advantageous in environments where downtime is critical. They enhance operational efficiency by reducing the time needed for fluid maintenance. However, this type may have disadvantages concerning sealing capability compared to standard caps, as their quick release feature might not effectively maintain pressure in some systems. Regular assessment for wear and tear is advisable to mitigate any risks associated with their use.
Design Considerations
Design considerations are vital for optimizing the performance and reliability of hydraulic oil filler caps. These elements influence not only the longevity of the caps but also the overall efficiency of the hydraulic systems in which they are used. The right design choices can prevent common issues such as leaks and contamination while enhancing the ease of maintenance. Each aspect of the design should be thoughtfully evaluated to effectively serve its purpose within demanding farming environments.
Material Selection
Plastic vs. Metal
When discussing material selection, it is essential to compare plastic with metal for hydraulic oil filler caps. Plastics, often lightweight and cost-effective, are frequently used due to their resistance to rust and easier injection molding capabilities. They can be manufactured with complex geometries that suit various applications. However, plastics may not withstand extreme temperatures as well as metals. On the other hand, metal caps boast significant strength and durability, making them suitable for heavy-duty machines. Metal options usually feature higher resistance to mechanical damage and can endure more demanding conditions, which may be essential in agricultural tasks.
Choosing between plastic and metal requires assessing the specific operational environment and requirements. The application involves balancing costs with the required durability level, considering how each material contributes to the cap's effectiveness in sealing and protecting hydraulic fluid.
Durability and Corrosion Resistance
Durability and corrosion resistance are critical aspects in the longevity of hydraulic oil filler caps. Durable materials extend the lifespan of components in hydraulic systems, minimizing the need for regular replacements. This quality is particularly important for applications in areas exposed to harsh weather or corrosive environments. For instance, a cap that can resist corrosion will prevent fluid contamination, which can significantly affect system performance.
The emphasis on corrosion resistance should be prioritized to reduce maintenance costs. In agricultural settings, where equipment must endure rain, mud, and chemical fertilizers, selecting materials known for high corrosion resistance can drastically enhance operational efficiency. The right choices here not only ensure reliable performance but also minimize downtime caused by maintenance issues.
Seal and Closure Mechanisms
Effective seal and closure mechanisms are essential for maintaining hydraulic systems. They help ensure that the hydraulic oil filler cap remains securely in place, preventing leaks and contamination from external particles. Different mechanisms, such as threaded closures, snap-on designs, or locking systems, offer various advantages.
Using proper seals is fundamental to maintaining fluid integrity. Material selection for seals also plays a pivotal role, as some materials perform better in resisting temperature fluctuations and chemical exposure than others. Regular examination of these components ensures that hydraulic oil filler caps function as intended, providing optimal protection for hydraulic fluid.
Maintenance of Hydraulic Oil Filler Caps
Maintaining hydraulic oil filler caps is essential for the integrity and efficiency of hydraulic systems. These components play a pivotal role in ensuring that hydraulic fluids remain uncontaminated and properly pressurized. Failing to maintain them can lead to leaks, which decrease the system's effectiveness and can cause extensive damage in agricultural machinery and horticultural equipment. Hence, proactive maintenance can prevent costly repairs and prolong the lifespan of hydraulic systems.
Regular Inspection
Regular inspections of hydraulic oil filler caps should be an integral part of maintenance protocols. During inspections, operators should look for signs of wear, corrosion, or any visible damage. Checking the seal integrity is key. A compromised seal can lead to fluid leakage or contamination. Additionally, operators should ensure that the cap fits snugly. A loose cap can cause air to enter the system, leading to cavitation or reduced pressure. Performing these inspections periodically, ideally before and after usage, helps catch potential issues early.
Cleaning Procedures
Cleaning hydraulic oil filler caps should be done carefully to avoid introducing contaminants into the hydraulic system. Operators should use a clean lint-free cloth or a designated cleaning tool to wipe down the outside of the cap and the filler neck. It is important to remove any dirt or debris that might interfere with the seal of the cap. In cases where fluid has spilt, it is critical to clean it immediately to avoid contamination of the hydraulic oil. However, one must avoid using strong solvents or harsh chemicals, as these can degrade the materials of the cap and surrounding components.
Replacement Indicators
Knowing when to replace hydraulic oil filler caps is vital for maintaining system performance. Key indicators include visible cracks or deformation on the cap itself. Additionally, a cap that does not provide a secure fit may require replacement. Users should also consider the age of the cap; if a cap has been in service for many years or cycles, it might be prudent to replace it during routine maintenance. Lastly, any signs of persistent leaks around the cap area should trigger an evaluation for replacement.
"Proper maintenance of hydraulic oil filler caps is not just about extending the life of the parts, but safeguarding the entire hydraulic system from potential failures."
Common Issues and Troubleshooting
Understanding the common issues related to hydraulic oil filler caps is essential for maintaining the efficiency of hydraulic systems, particularly in agricultural and horticultural applications. Identifying potential problems early can prevent costly repairs, downtime, and operational inefficiency. This section will delve into two primary issues: leakage problems and cap damage. Each subsection will explore the nature of these issues and provide insights into troubleshooting methods.
Leakage Problems
Leakage is one of the most prevalent issues encountered with hydraulic oil filler caps. This problem can occur for several reasons, each contributing to fluid loss, which can lead to reduced hydraulic pressure and performance. Here are some key factors to consider:
- Worn Seals: Over time, seals within the cap may wear due to continuous exposure to hydraulic oil and environmental elements. This degradation can cause oil to seep out.
- Improper Installation: If the hydraulic oil filler cap is not installed correctly, it may not create a proper seal, allowing fluid to escape.
- Temperature Fluctuations: Extreme temperature changes can cause materials to expand and contract, which can lead to leakage if the cap is compromised.
To troubleshoot leakage problems, conduct regular inspections to check for signs of oil accumulation around the filler cap area. Applying slight pressure to the cap while checking the seals can also help identify if they are functioning well. In some cases, replacing the seals or the entire cap may be necessary for a long-lasting solution.
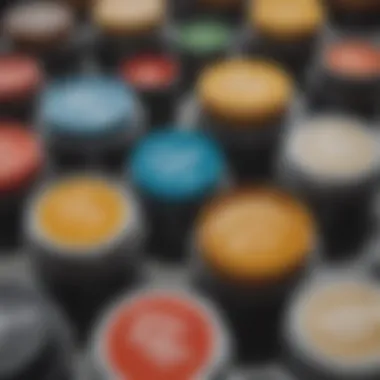
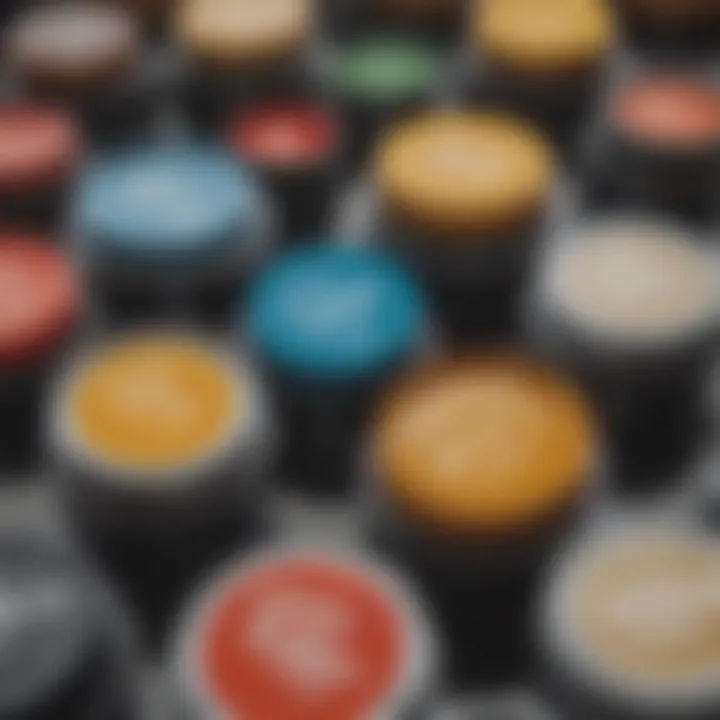
"Regular maintenance and inspection can significantly mitigate the risks of hydraulic oil leakage, ensuring smooth operation for your equipment."
Cap Damage
Cap damage can manifest in various forms, including cracks, deformation, or complete breakage. Identifying and addressing cap damage promptly is critical to maintaining hydraulic system integrity. Some common causes of cap damage include:
- Physical Impact: Accidents during machinery operation may lead to the cap being struck or knocked off, resulting in damage.
- Corrosive Environments: Hydraulic systems often operate in challenging conditions. Exposure to harsh chemicals and prolonged moisture can weaken the cap material, leading to cracks or failure.
- Improper Handling: Mishandling during maintenance or filling can lead to immediate damage or weaken the cap over time.
When assessing cap damage, visually inspect the cap for visible cracks or distortions. A damaged cap should be replaced immediately to avoid further issues like contamination or hydraulic failure. Ensuring that the right cap is chosen based on material compatibility and application-specific requirements can significantly reduce the risk of future problems.
Applications of Hydraulic Systems
The applications of hydraulic systems are integral to various industries, particularly in agriculture and horticulture. These systems are characterized by their ability to transmit power through incompressible fluids, which allows for the operation of machinery with high efficiency and reliability. Understanding the specific applications is crucial not only for optimizing performance but also for ensuring the longevity of equipment and systems in use.
In Agricultural Machinery
Agricultural machinery relies heavily on hydraulic systems to facilitate numerous operations, such as planting, harvesting, and spraying. The efficiency of hydraulic systems in these machines comes from their capability to generate significant force while maintaining precise control. For instance, tractors equipped with hydraulic lift systems can raise and lower heavy implements effortlessly.
- Efficiency in Field Operations: The use of hydraulic systems allows for quick and versatile adjustments during fieldwork. Hydraulic implements can be changed or modified with ease, enabling farmers to adapt to various tasks without the need for additional equipment.
- Powerful Lifting Capabilities: Hydraulic lifts can effectively handle heavy loads, reducing physical strain on the operator. This capability is particularly beneficial in large-scale agricultural operations where heavy machinery and materials are commonplace.
- Precision and Control: Hydraulic systems enable precise movements, which is necessary for tasks like planting seeds at specific depths. This precision enhances crop yields while minimizing waste.
In Horticultural Equipment
Horticultural equipment frequently utilizes hydraulic systems for their need for intricate control and versatility in various tasks. In many cases, the goal is to maintain delicate balance and accurate movements, which hydraulic technology provides effectively.
- Greenhouse Automation: Hydraulic systems are used in automated greenhouse environments to control curtains, vents, and irrigation systems. This automation increases operational efficiency and optimizes growing conditions.
- Trimming and Pruning Equipment: In horticulture, machinery such as hydraulic pruners can facilitate precise cuts without harming the plant. This capability is essential for maintaining plant health and promoting growth.
- Mobility Solutions: Hydraulic systems allow for the customization of mobile equipment, such as lift tables and harvesters. The flexibility provided by hydraulics enhances a grower's ability to maneuver through various terrains and workspaces.
Overall, hydraulic systems serve vital roles in agricultural and horticultural applications, offering benefits like increased efficiency, enhanced control, and adaptability. These factors not only contribute to sustainable practices but also improve the overall productivity of farms and gardens, underscoring the importance of integrating effective hydraulic solutions into modern agricultural practices.
Hydraulic systems are not just mechanical solutions; they are pivotal in transforming traditional practices into modern, efficient methodologies.
Future Trends in Hydraulic Technology
The field of hydraulic technology is evolving rapidly, with new advancements poised to transform how hydraulic systems operate. Understanding these future trends is essential for farmers and horticultural enthusiasts who rely on hydraulic machinery for their day-to-day operations. These developments promise to enhance performance, reduce environmental impact, and lead to greater overall efficiency. As the agricultural sector continually seeks improvements in productivity and sustainability, being aware of these trends becomes increasingly important.
Advancements in Materials
One of the most significant areas of progress in hydraulic technology is the development of advanced materials. These materials are engineered to offer better durability, corrosion resistance, and weight efficiency. For example, materials like high-strength polymers and composite materials are being used to create hydraulic components that are both lighter and stronger than traditional metals.
- Benefits of advanced materials:
- Reduced Weight: Lighter components can enhance fuel efficiency in machinery.
- Improved Performance: Resistance to wear and tear prolongs the lifespan of hydraulic parts.
- Sustainability: Many new materials are sourced sustainably or are recyclable, aligning with the growing focus on environmental stewardship.
The development of biodegradable hydraulic fluids is also noteworthy. These fluids minimize the ecological footprint of hydraulic systems, providing a safer alternative while maintaining the required performance standards.
Increased Efficiency and Sustainability
Efficiency and sustainability are at the forefront of modern agricultural practices. Hydraulic systems are increasingly designed with these principles in mind. Innovations such as the integration of smart controls and sensors into hydraulic systems are becoming common. These technologies allow for real-time monitoring and adjustments, leading to more efficient operation while minimizing wastage.
- Key aspects of efficiency and sustainability include:
- Optimized Hydraulic Fluid Usage: Reducing the quantity of hydraulic fluids through better design and control leads to less environmental impact.
- Energy Recovery Systems: These systems capture and reuse energy that is typically lost in hydraulic operations, promoting sustainable machinery use.
- Advanced Leak Detection: Sensors can identify potential leaks early, which helps in preventing fluid loss and maintaining system integrity.
These trends signal a shift towards more responsible farming practices that not only improve operational efficiency but also reduce environmental harm. As the agriculture sector increasingly emphasizes sustainable practices, the adoption of these advancements will likely become essential for success in an increasingly competitive market.
Finale
The conclusion section holds great importance in bringing together the varied elements discussed in this article. A thorough understanding of hydraulic oil filler caps is essential for anyone involved in agriculture and horticulture. It serves as a summary of the core concepts regarding the functions, maintenance, and applications of these caps.
Hydraulic oil filler caps, while seemingly simple components, play a vital role in the overall efficiency and reliability of hydraulic systems. They ensure that hydraulic fluids remain contained and uncontaminated, impacting the longevity and performance of agricultural machinery. Proper maintenance and timely inspection of these caps can prevent costly downtime and enhance productivity.
Furthermore, recognizing common issues associated with hydraulic oil filler caps, such as leakage and damage, positions farmers and equipment operators to address problems proactively. The applications of these systems in both agriculture and horticulture highlight their versatility and significance in modern farming practices.
In summary, understanding the nuances of hydraulic oil filler caps encourages better maintenance practices and promotes informed decision-making. By acknowledging their vital functions and addressing maintenance concerns, agricultural professionals can harness the full potential of hydraulic systems, leading to more sustainable and efficient farming operations. The insights shared throughout this article ultimately underscore the need for continuous learning and adaptation in this field.
"Effective maintenance of hydraulic systems leads to increased productivity and reduced operational costs."
In essence, a comprehensive grasp of hydraulic oil filler caps assists with the overall goal of achieving excellence in agricultural practices.