Hydraulic Oil Pressure in Agricultural Machinery

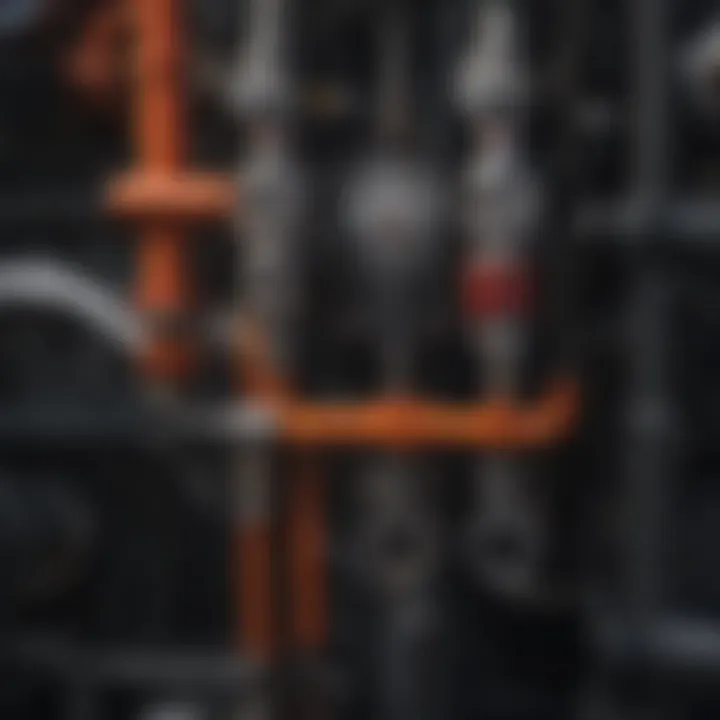
Intro
The role of hydraulic oil pressure in agricultural machinery is both vital and often overlooked. Hydraulic systems are the backbone of many machines used in farming, influencing their efficiency and overall performance. When hydraulic oil pressure is within the optimal range, machinery operates smoothly, ensuring effective task completion. Conversely, improper pressure levels can lead to costly downtime and increased maintenance. Understanding these dynamics is essential for anyone involved in agricultural operations.
This article will explore key aspects of hydraulic oil pressure, focusing on its impact on performance, efficiency, and maintenance. We will examine the mechanisms of hydraulic systems, the significance of maintaining optimal pressure levels, and the potential challenges faced by operators. Key factors affecting hydraulic oil pressure will be discussed, along with troubleshooting common issues and emerging technologies in hydraulic systems. By the end of this exploration, readers should gain a thorough knowledge of how to operate and maintain hydraulic systems effectively in agriculture.
Latest Trends in Agriculture
Overview of Current Trends
Agricultural practices are evolving, driven by advancements in technology and a greater focus on sustainability. Farmers are increasingly adopting precision farming techniques, which rely on data analytics and advanced machinery. These approaches help optimize the usage of resources such as water and fertilizers, ensuring that farmers can maximize yields while minimizing costs. Hydraulic systems in modern tractors and harvesters are incorporating greater automation and control, allowing for more precise operations.
Impact of Technology on Farming Practices
The integration of technology in agriculture does not stop at machinery. It extends to hydraulic systems as well. Innovations such as smart sensors and IoT technology are helping farmers monitor hydraulic oil pressure in real-time. This allows for adjustments to be made on the fly and can prevent issues before they arise. Keeping track of these parameters helps in understanding when maintenance is needed, ultimately leading to better performance and reduced risk of failure.
"Efficient hydraulic systems are crucial for the seamless operation of agricultural machinery, impacting everything from planting to harvesting."
Sustainable Practices: Towards a Greener Future
Importance of Sustainability in Agriculture
Sustainability is now at the forefront of many discussions in agriculture. Farmers are being encouraged to adopt practices that reduce environmental impact. Hydraulic systems contribute to this by using pressure management techniques that optimize fuel efficiency and reduce emissions.
Methods for Sustainable Farming
Several methods can be utilized to ensure sustainable practices:
- Crop Rotation: Enhances soil health and reduces pests.
- Tillage Reduction: Minimizes soil disturbance, helping maintain its structure.
- Efficient Water Use: Utilizes hydraulic systems to manage irrigation effectively.
By integrating sustainable methods, farmers can ensure their operations are not only effective but also environmentally friendly.
Ending
Foreword to Hydraulic Systems
Hydraulic systems are integral to many forms of agricultural machinery, providing the necessary power to perform various functions with precision and efficiency. Understanding this foundational concept enables users to maximize their machinery's potential and uphold performance standards.
In this section, we focus on the fundamental aspects of hydraulic systems, starting with a clear definition followed by an exploration of their primary components. Each component plays a vital role in ensuring the hydraulic system operates optimally, and neglecting any one part may lead to operational issues.
Definition of Hydraulic Systems
A hydraulic system uses pressurized fluid to transmit power. The key principle revolves around the incompressibility of liquids, which allows for force transmission. When force is applied to the fluid in one part of the system, it is transmitted throughout the system, leading to movement and operation of machinery without the need for mechanical linkages.
The hydraulic system’s design supports heavy lifting and precise control, making it a preferred choice in agricultural applications, from tractors to harvesters. Understanding this definition sets the groundwork for delving deeper into the specifics of how these systems function and why they are so critical in agriculture.
Components of Hydraulic Systems
Hydraulic systems consist of several key components, each serving an essential purpose. The components include:
Pump
The pump is crucial in any hydraulic system as it generates the pressure needed to move the hydraulic fluid. A hydraulic pump converts mechanical energy into hydraulic energy. Its efficiency directly impacts the overall performance of the system, affecting how well the machinery operates. A common choice is the gear pump because of its reliability and ability to handle high pressures.
However, an important unique feature of pumps is their vulnerability to wear, especially when operating under high speeds or with contaminated oil. Regular inspection and maintenance must be performed to avoid performance degradation.
Valves
Valves control the flow and direction of the hydraulic fluid. They ensure that the correct amount of power reaches the components that need it. The directional control valve, for instance, is a popular type which allows operators to select multiple functions as needed. Its key characteristic is the flexibility it offers in operation, enabling the user to manipulate movements precisely.
Yet, a downside is the possibility of leaks if not maintained properly, leading to power losses and potential system failure.
Cylinders
Hydraulic cylinders provide linear motion by converting fluid pressure into mechanical force. They are the systems’ actuators, pushing or pulling components to accomplish tasks. The double-acting hydraulic cylinder is widely used as it can exert force in both directions, a key benefit in many agricultural applications like lifting and pushing.
However, like pumps, cylinders can also face issues such as seal failure, which can lead to drops in pressure and performance.
Reservoir
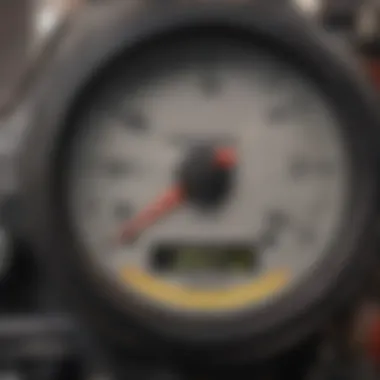
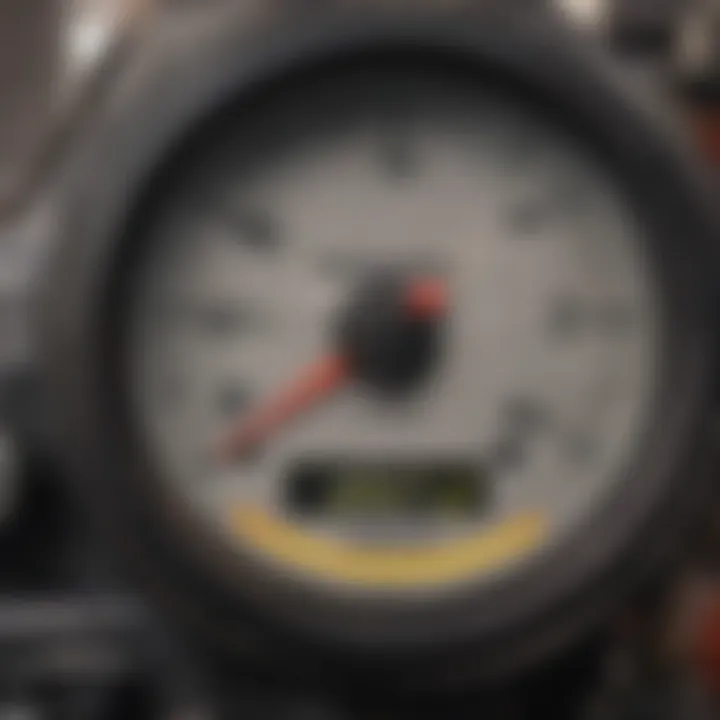
This component stores hydraulic fluid, allowing the system to operate efficiently by supplying oil as needed. A reservoir also helps in heat dissipation and prevents contamination by allowing particulates to settle. Its key characteristic is the size, which needs to be adequate to ensure proper fluid supply during operations.
One unique feature is the presence of a filtration system within the reservoir. While it ensures cleaner fluid is used within the system, a complex filtration setup may raise maintenance challenges, necessitating regular checks to sustain optimal functionality.
Understanding Hydraulic Oil Pressure
Hydraulic oil pressure is a crucial element in the efficiency and performance of agricultural machinery. Understanding it means recognizing its role in generating power and controlling equipment effectively in the field. Without adequate pressure, machines can underperform, leading to reduced productivity and increased maintanance costs. Thus, grasping the concept of hydraulic oil pressure is essential for farmers and enthusiasts looking to enhance their operational capabilities.
Importance of Oil Pressure
Oil pressure serves multiple functions within hydraulic systems. It enables movement and power transfer, directly impacting how machinery operates. Without the right pressure, tasks such as lifting, pushing, and turning cannot be executed efficiently. The stability of oil pressure is also important. It ensures the machinery can handle varying loads and adapt to different operational scenarios. In short, maintaining optimal oil pressure is central to achieving the best performance in various agricultural tasks.
How Pressure is Generated
Generaating hydraulic pressure is an interplay of several mechanical and fluid dynamics processes. Customarily, this generation occurs through specific actions within the hydraulic system that convert mechanical energy into hydraulic energy.
Mechanical Actions
Mechanical actions are fundamental in creating hydraulic oil pressure. When energy is applied to a pump, it causes the hydraulic fluid to move, creating pressure. This movement is often initiated by the engine's power being transferred to the hydraulic pump. A key characteristic of mechanical actions is their ability to deliver rapid and precise force. This aspect makes such actions a popular choice for agricultural machinery since they can adjust quickly to changing demands on the equipment.
The unique feature of mechanical actions lies in their direct relationship to engine power. When functioning correctly, a hydraulic system can respond to different load conditions by adjusting the oil pressure, thereby enhancing performance. However, mechanical actions also present potential disadvantages, such as increased wear and tear on components over time, necessitating regular inspections and maintenance.
Fluid Dynamics
Fluid dynamics plays a critical role in maintaining hydraulic oil pressure. It involves the study of how fluids behave when they are in motion. A significant aspect of fluid dynamics in hydraulic systems is understanding how momentum and resistance affect pressure levels. The viscosity of the hydraulic fluid and the size of the pipes influence this behavior.
A key characteristic of fluid dynamics is its ability to optimize the flow of hydraulic oil. This optimization is vital since it ensures that all components receive the necessary pressure to function efficiently. The unique feature of fluid dynamics is the concept of laminar versus turbulent flow, where controlled flow can lead to better pressure maintenance.
While fluid dynamics offers advantages in terms of reducing energy losses and enhancing system efficiency, it can be sensitive to changes in temperature. Fluctuations in temperature can affect viscosity, impacting overall system performance. Therefore, awareness of how fluid dynamics operates is essential for anyone managing hydraulin systems in agricultural contexts.
Optimal Pressure Levels
Understanding optimal pressure levels in hydraulic systems is crucial for effective operation in agricultural machinery. Proper hydraulic oil pressure ensures that equipment operates smoothly, handles loads efficiently, and responds well to user commands. Maintaining the right pressure level can extend the life of components and prevent costly repairs.
Standard Operating Pressures
Standard operating pressures in hydraulic systems typically range from 1500 to 3000 psi, depending on the machinery and application involved. These figures represent an average that supports sufficient torque and lifting capabilities while preventing excess wear on the system. Each piece of equipment may have its specifications, so consulting the user manual or manufacturer guidelines is essential.
Being within the standard pressure range helps in achieving a balance between performance and safety. If the system operates below this range, equipment efficiency declines.
Effects of Low Pressure
When hydraulic oil pressure drops below the standard levels, it can lead to several complications. Some common effects include:
- Decreased Performance: Machines cannot operate at full capacity. Tasks take longer and may require more effort from the operator.
- Slow Response Time: Actuation of hydraulic components becomes sluggish, which can affect overall productivity.
- Overheating: Low pressure can cause parts to work harder, generating heat and potentially leading to failures.
In agricultural applications, low pressure may hinder clutch engagement or alter the hydraulic flow, damaging the equipment in the long run.
Effects of High Pressure
Conversely, operating above the recommended pressure levels can also bring significant issues. Some potential problems caused by high pressure include:
- Increased Wear: Components are subjected to excessive stress, leading to premature failure and breakdowns.
- Safety Risks: High-pressure hydraulic systems can be dangerous. Burst hoses or failing components can cause injuries.
- Pressure Relief System Activation: Systems designed to manage pressure may engage more often, which can lead to leaks or inefficiencies.
For these reasons, understanding the balance of hydraulic oil pressure is essential for anyone involved in the operation and maintenance of agricultural machinery.
It is important to regularly monitor pressure levels to catch any deviations from normal operating conditions early on.
Factors Influencing Hydraulic Oil Pressure
Understanding the factors that influence hydraulic oil pressure is essential for maintaining optimal performance and efficiency in agricultural machinery. Various elements affect the hydraulic oil pressure, and recognizing these can enhance system effectiveness, reduce wear, and prolong the life of equipment. This section examines three primary factors—temperature effects, viscosity of hydraulic oil, and system load conditions. Addressing these elements ensures better operation and reliability.
Temperature Effects
Temperature plays a critical role in hydraulic oil performance. As temperatures rise, hydraulic oil expands, which can lead to a decrease in viscosity. This thinner oil may result in reduced lubrication for components, higher wear rates, and increased risk of system failure. Conversely, low temperatures can thicken the oil, making it more viscous and harder to pump. This can create additional strain on the hydraulic pump and lead to inadequate system response.
Maintaining the hydraulic oil at the correct temperature is essential. Extreme temperatures, both high and low, can severely impact hydraulic oil pressure and overall system reliability.
Operators should routinely check system temperatures, ensuring they fall within the manufacturer’s recommended range. Implementing temperature monitoring systems can assist in maintaining these levels, fostering better hydraulic system integrity.
Viscosity of Hydraulic Oil
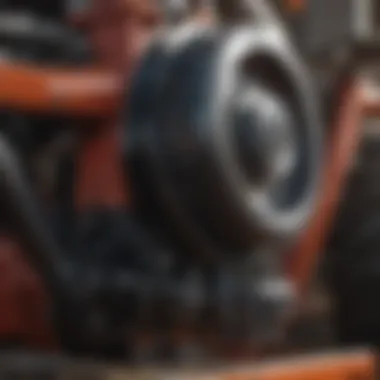
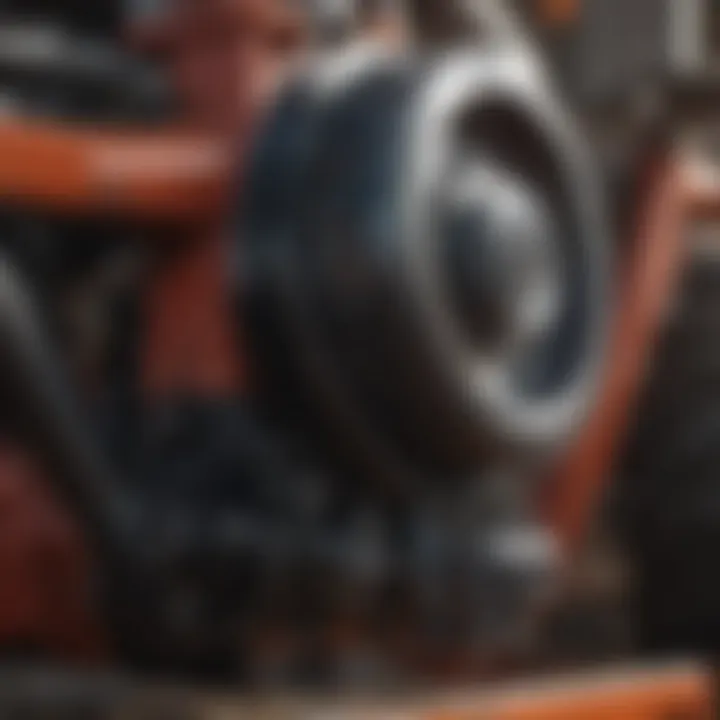
Viscosity is a measure of a fluid's resistance to flow. Hydraulic oil with proper viscosity ensures adequate lubrication and proper functioning of hydraulic components. The viscosity of the hydraulic oil can change with temperature; in high heat, the oil becomes thinner, whereas in cold conditions, it becomes thicker. Using oil with the right viscosity for specific temperatures is necessary for effective hydraulic pressure management.
When selecting hydraulic oil, look for the manufacturer’s specification. Using oils with inappropriate viscosity can lead to system inefficiency and even failure.
- Low Viscosity: Can cause loss of pressure and increased leakage.
- High Viscosity: Might result in hard starting and inefficient operation.
Regular oil analysis is advised to ensure viscosity remains optimal, especially in varying temperature conditions.
System Load Conditions
The load conditions of the hydraulic system significantly influence oil pressure. When equipment operates under high loads, the hydraulic pressure increases to meet the demand. Conversely, lighter loads require less pressure. It is critical to design hydraulic systems that can handle varying load conditions effectively.
Operators should monitor the load on hydraulic systems. Regular adjustments may be needed to balance performance and pressure. Understanding how load conditions affect pressure helps in predicting system requirements and managing efficiencies.
- Overloading can lead to pressure spikes, risking device failures.
- Underloading may not efficiently utilize power.
By grasping and managing these factors, agricultural operators can ensure smoother hydraulic operation, reducing maintenance needs and unauthorized downtime.
Common Issues in Hydraulic Systems
Understanding the common issues in hydraulic systems is essential for maintaining the efficiency and safety of agricultural machinery. Hydraulic systems are integral for various tasks in farming, relying heavily on the proper functioning of hydraulic oil pressure. When problems arise, they can lead to significant operational setbacks, impacting productivity and costs.
Leakage Problems
Leakage is one of the most prevalent problems encountered in hydraulic systems. When hydraulic fluid leaks, it reduces the overall fluid volume, which can directly lower the oil pressure. This reduction can lead to improper function of hydraulic cylinders and motors, causing machines to operate ineffectively. Common sources of leaks include damaged hoses, loose fittings, and degraded seals.
To prevent leakage issues, regular inspection of hydraulic components is crucial. Additionally, using quality hoses and fittings can reduce the risk of leaks. Addressing leaks promptly not only preserves hydraulic efficiency but also prevents potential safety hazards.
Contamination of Hydraulic Oil
Contamination is another critical issue that affects hydraulic oil pressure. Hydraulic oil can become contaminated due to dirt, moisture, or other substances entering the system. Contaminants can lead to increased wear of components, resulting in reduced efficiency and potential system failures. Water, for example, can cause rust, while dirt can act as an abrasive, damaging critical parts.
Regular oil analysis and proper filtration can help maintain oil purity. Farmers should also implement best practices, like preventing dirt ingress when changing hydraulic oil. This attention to cleanliness can extend the life of both the hydraulic oil and the system components.
Failure of Components
Component failure can occur for various reasons, including fatigue, improper maintenance, or exceeding operational limits. When a hydraulic component fails, it can disrupt the entire system, leading to loss of pressure and function. Commonly affected components include pumps, valves, and cylinders.
To mitigate the risk of component failure, farmers should adhere to a strict maintenance schedule. This includes regular inspections and timely replacement of worn-out parts. Understanding the operational limits of each component can also prevent undue stress and enhance system longevity.
"Maintaining hydraulic systems through regular inspections, oil purification, and timely replacements is fundamental for optimal performance."
By addressing these common issues proactively, agricultural producers can ensure their hydraulic systems operate smoothly and efficiently, thus sustaining productivity in their operations.
Troubleshooting Hydraulic Oil Pressure Issues
In agricultural machinery, hydraulic systems play a vital role in functionality and efficiency. Troubleshooting hydraulic oil pressure issues is essential for optimal performance. When problems arise, addressing them promptly can prevent more significant failures and costly repairs. Understanding symptoms of pressure issues helps farmers identify the problem early. For this reason, troubleshooting requires systematic analysis.
Identifying Symptoms
Common symptoms of hydraulic oil pressure problems vary. Noticing a drop in performance can be the first red flag. Equipment may operate slower than usual or exhibit jerky movements. Aside from performance issues, listening to unusual noises is crucial. Whining or grinding sounds can indicate pressure irregularities. Leaks around hydraulic lines and fittings are another physical symptom to watch for. Any visible oil may signal a significant problem needing immediate attention.
Diagnostic Tools
Pressure Gauges
Pressure gauges are essential tools for evaluating hydraulic systems. They measure the hydraulic oil pressure and provide immediate feedback. One key characteristic of pressure gauges is their accuracy. This accuracy makes them a beneficial choice for diagnosing hydraulic issues. The unique feature of many gauges is their ability to provide real-time monitoring. This advantage allows farmers to make adjustments quickly. However, they also have disadvantages. If damaged, they can give false readings, leading to improper assessments of the system.
Flow Meters
Flow meters help in assessing the flow rate of hydraulic oil through the system. Monitoring flow is vital for understanding how well the system operates. A key characteristic of flow meters is that they can measure both the rate and volume of oil. This aspect makes them an effective diagnostic tool for evaluating system performance. The unique feature of flow meters is their ability to analyze oil movement. This helps in identifying blockages or flow restrictions. An advantage is that they can provide a comprehensive understanding of system dynamics. However, they require regular calibration to ensure accuracy, which may be a disadvantage for some users.
Steps for Resolution
Resolving hydraulic oil pressure issues involves a systematic approach. First, gather data by observing symptoms to identify pressure inconsistencies. Next, conduct measurements using tools like pressure gauges and flow meters. This data identifies specific problems. Following identification, evaluate the system's components to find potential faults. This may include checking for leaks or examining filters and hoses. Consider replacing components that show signs of wear. Finally, perform routine maintenance to prevent future issues and ensure long-lasting efficiency.
Maintenance Practices for Hydraulic Systems
Maintaining hydraulic systems is essential for the effective performance of agricultural machinery. Regular upkeep can prevent costly downtimes and extend the lifespan of hydraulic components. Proper maintenance practices help ensure the system operates within its optimal hydraulic oil pressure range. This section will discuss the key maintenance tasks: regular inspection, oil changes, and component replacement.

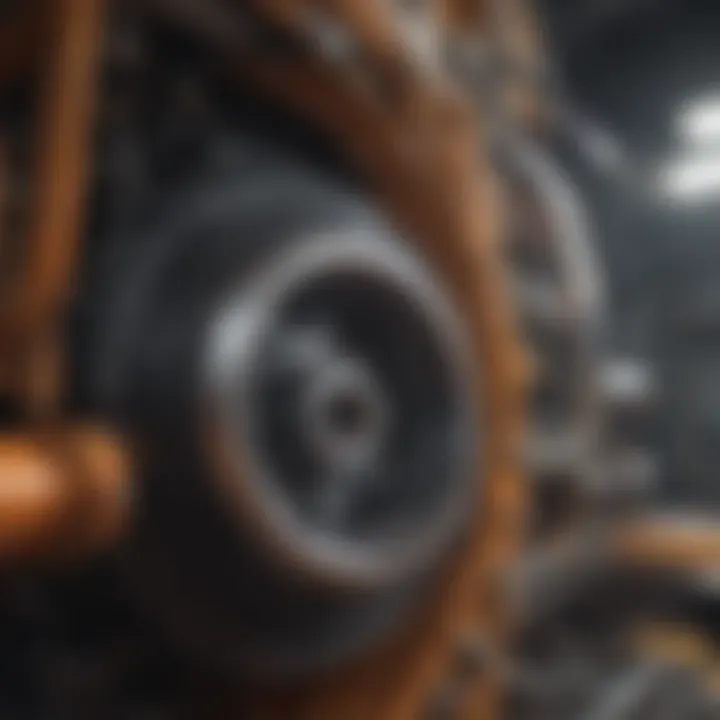
Regular Inspection
Regular inspection of hydraulic systems is vital. It allows operators to detect potential issues before they escalate. Inspections should focus on several components, including hoses, fittings, and seals. Look for signs of wear, leaks, and corrosion. By identifying these problems early, it is possible to avoid unplanned equipment failures.
Regular inspections also include checking hydraulic oil levels and monitoring system performance. Operators should refer to the manufacturer’s guidelines regarding recommended inspection intervals. Documenting findings from inspections helps track the system’s condition over time. This practice creates awareness of patterns that may indicate deeper issues.
Oil Changes
Hydraulic oil plays a crucial role in the function of hydraulic systems. Over time, oil can become contaminated with dirt, water, and metal particles. Therefore, it is essential to change the hydraulic oil at regular intervals. Operators should refer to the machinery manufacturer’s specifications for recommended oil change frequency.
Benefits of timely oil changes include:
- Reduced wear and tear on components
- Improved efficiency
- Enhanced cooling properties of the hydraulic system
When changing oil, it is necessary to dispose of the old oil responsibly. Used hydraulic oil can be harmful to the environment. Operators should ensure compliance with local regulations regarding disposal methods.
Component Replacement
Despite regular maintenance, some components may eventually wear out and need replacement. Identifying when to replace parts is critical to maintaining system performance. Key components such as pumps, valves, and cylinders should be checked frequently for any signs of malfunction.
Replacement should be performed using quality parts that adhere to the machinery specifications. The steps for successful component replacement may include:
- Powering down the system and relieving pressure.
- Removing the faulty component carefully.
- Installing the new component properly, ensuring all connections are secure.
- Testing the system to ensure proper operation.
By following these maintenance practices, operators can significantly reduce the risk of hydraulic oil pressure issues in agricultural machinery. Regular inspection, timely oil changes, and appropriate component replacement contribute to a reliable and efficient agricultural operation.
"Effective maintenance is a proactive approach that safeguards hydraulic system integrity and performance."
Ensuring that hydraulic systems are maintained efficiently will enable agricultural equipment to work effectively in various conditions. This reduces overall maintenance costs and improves productivity.
Advancements in Hydraulic Technology
The landscape of agricultural machinery is continually evolving. At the core of this change is the advancement in hydraulic technology. It plays a pivotal role in maintaining efficiency and performance in agricultural operations. By understanding these advancements, farmers can improve productivity and reduce operational costs.
Smart Hydraulic Systems
Smart hydraulic systems represent a significant leap forward in the agricultural sector. These systems utilize sensors and data analytics to optimize performance in real-time. For instance, sensors monitor hydraulic oil pressure, temperature, and flow rates. This data enables proactive adjustments. The goal is to maintain the optimal pressure levels essential for machine efficiency.
Farmers can benefit greatly from these systems. They provide detailed reports on machinery performance. This information helps in identifying potential issues before they become significant problems. For example, early detection of low pressure can alert operators to leaks or mechanical failures. Adaptation of this technology can lead to a decrease in unplanned downtime and maintenance costs.
Energy Efficiency Innovations
Energy efficiency is a key concern in modern agriculture. Innovations in hydraulic technology focus on reducing energy consumption while maintaining performance. Variable displacement pumps are one such innovation. They adjust the flow of hydraulic fluid based on demand. This means using only the necessary amount of energy for the task at hand.
Moreover, using biodegradable hydraulic oils reduces environmental impact. Many farmers are now opting for theses sustainable options. They retain the necessary performance characteristics without the negative environmental effects associated with traditional oils.
The benefits extend beyond environmental considerations. Improved energy efficiency translates to lower operational costs. This can lead farmers toward more sustainable practices.
Future Trends in Agricultural Hydraulics
Looking ahead, several trends are emerging in hydraulic technology. Automation is becoming more prevalent. This will likely include integration with precision farming techniques. The use of drones for monitoring hydraulic performance is one potential development.
Further exploration into alternative energy sources is expected. Hydraulic systems might use electric power or even solar energy, reducing reliance on fossil fuels. Such innovation can make agricultural practices more environmentally friendly.
Adopting these technologies is not without challenges. Farmers must consider costs, training, and adaptation to new systems. However, the long-term benefits often outweigh these initial hurdles. By keeping abreast of these advancements, agricultural producers can stay competitive in a changing market.
In summary, advancements in hydraulic technology are redefining agricultural machinery. They offer opportunities for improved performance, reduced costs, and sustainable practices, making it essential for modern farmers to embrace these changes.
End
In reviewing the critical role of hydraulic oil pressure in agricultural machinery, it becomes evident that this topic is not merely specialized knowledge but essential for anyone involved in the management or operation of these systems. The hydraulic oil pressure influences performance, efficiency, and longevity, all key components that determine the productive capability of agricultural operations.
Summary of Key Points
Several key points have emerged throughout this article:
- Hydraulic Systems Basics: Understanding the foundational elements of hydraulic systems can greatly aid in recognizing how pressure is generated and regulated.
- Optimal Pressure Levels: Maintaining standard operating pressures ensures that equipment functions efficiently, preventing issues related to both low and high pressures.
- Influencing Factors: Factors such as temperature, oil viscosity, and the load conditions of the system play a significant role in the performance of hydraulic oil pressure.
- Common Issues and Maintenance: Identifying common problems like leakage and contamination promptly helps in maintaining system integrity and functionality.
- Advancements in Technology: New trends such as smart hydraulic systems and innovations geared towards energy efficiency show promise for the future of agricultural hydraulics.
Final Thoughts on Hydraulic Oil Pressure in Agriculture
The significance of hydraulic oil pressure in agriculture extends beyond basic comprehension. It encapsulates the machinery's effective operation brining efficiency and reliability in farming activities. As farmers and machinery operators deepen their understanding of hydraulic systems, they take substantial steps towards optimizing performance, reducing downtime, and ultimately enhancing productivity.
As technology advances, staying informed about innovations in hydraulic technology will further empower users to maintain and improve their hydraulic systems, leading to better agricultural practices and outcomes. The link between hydraulic oil pressure and successful agricultural operations is clear, warranting careful attention and strategic planning in all hydraulic machinery applications.
"Understanding and maintaining hydraulic oil pressure is crucial for maximizing efficiency in agricultural machinery."
Through ongoing education and proactive maintenance, professionals in the agricultural sector can now harness the full potential of their hydraulic systems, paving the way for a more productive and sustainable future.